VFD's Motor Control
New CFW900 Variable Speed Drive
The CFW900 VSD is the most innovative product for driving and
controlling motors in industrial machines and processes.
The CFW900 is a high-tech VSD for driving and controlling three-phase induction and permanent magnet motors. It offers excellent static and dynamic performance and highly precise torque, speed and position control. It can be used in a wide range of applications due to its high overload capacity. Thanks to its technology, the CFW900 variable speed drive provides energy savings, safety, increased productivity and quality in the process network in which it is implemented.
Human-Machine Interface
The CFW900 HMI offers a smart, modern and easy-to-use interface with simple and fast interaction.
- Graphic HMI
- Detachable Keypad
- Selection of the Direction of Rotation
- Local/Remote Selection
- Bluetooth Connectivity®
- RTC – Real-time clock
- Start Key
- Stop Key
- JOG Key
Intelligent Thermal Management
Due to the constant evolution of industrial processes and machines, efficient and effective solutions are increasingly required. The CFW900 has a unique thermal management function that allows its use in environments with different temperatures. From an integrated system, the VSD can measure the ambient temperature and configure itself by varying its switching frequency, thus becoming a versatile VSD and enabling its use in different industrial applications.
Connectivity
The CFW900 can be connected to the main industrial communication networks without additional modules, as it has two switch Ethernet ports for EtherNet/IP, Modbus-TCP and MQTT communication, and a serial port (RS485) for Modbus-RTU communication.
The new CFW900 HMI with Bluetooth® connectivity is ideal for panel builders and technical assistants, as, in conjunction with the new WPS Mobile app, it allows parameter monitoring with customized layout and components as well as parameterization, backup, restoration of parameters, and more.
WEG High Performance Technology
Induction Motor
- Scalar: motor speed control with slip compensation.
- VVW (Voltage Vector WEG) – voltage vector control: motor speed control with automatic adjustment to load and power supply variations.
- Sensorless vector (without encoder) – induction motors: torque and speed vector control with excellent dynamic response, even at low speeds.
- Vector with encoder: the encoder module makes the interface between the CFW900 and the motor, providing a closed-loop speed and position control with excellent precision and dynamic response across the entire speed range (even with the motor stopped).
PM Motor
- VVW PM is a method to control permanent magnet motors. It is ideal for medium and high speed applications where the main requirement is energy efficiency, such as: fans, pumps and compressors.
Main Features
- Supply voltage:
- 200 to 240 V single- or three-phase: output current 4.6 to 10.0 A (1.1 to 2.2 kW - 1.5 to 3.0 hp);
- 200 to 240 V three-phase: output current 4.6 to 250 A (1.1 to 75 kW - 1.5 to 100 hp);
- 380 to 480 V three-phase: output current 2.8 to 242 A (1.1 to 132 kW - 1.5 to 200 hp).
- Small size for better use of panel space;
- USB port incorporated into the HMI;
- Increased processing capacity;
- Possibility of memory expansion with 8GB MicroSD Card with industrial temperature;
- IoT Product - Ready with MQTT protocol in standard product;
- IE2 efficiency rating (IE C 61800-9-2 / EN 50598-2);
- Integrated STO (Safe Torque Off) and SS1-t (Safe Stop 1 time controlled) functions.
Frequency Inverter - CFW11 Series
High Productivity & Savings for Your Business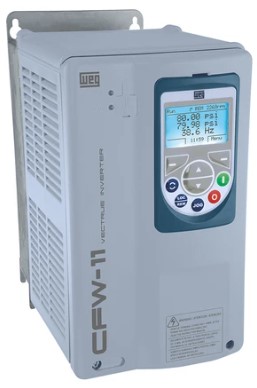
Offers high technology for control of three-phase induction motors and permanent magnets synchronous motors - Magnet. The CFW11 series achieves the performance increase for most complex drive systems. Design exclusive for industrial or professional use, the CFW11 presents many innovations adding significant benefits to customers, a lot for its simplicity of installation and operation, based in the Plug-and-Play philosophy also allowing simple and quick installation of its accessories in cluing a Remote Keypad which can be installed on panel doors or machine consoles with IP56 protection degree.
Vectrue Technology®
- Linear and adjustable V/F, VVW (Voltage Vector WEG) and vector control are available on CFW11
- Two types of vector control: sensor less and closed loop vector control (encoder Interface required)
- Sensor less vector control permits high torque and quick response in open loop, even at low speeds
- The self-tuning function sets the vector control or VVW with the motor and to application load used
- By the adjustable V/F control, it is possible, for example, to adjust a quadratic V/F curve, providing energy savings for quadratic torque loads (e.g.: centrifugal pumps and fans)
Optimal Braking®
Applications involving high inertia loads, when applied short time deceleration, a large amount of energy returns from the motor to the VSD. To handle this energy, regular VSDs have to dissipate it as heat in power resistors. Such resistors are usually large, and some installation criteria must be considered due to their heat dissipation. As an alternative to the use of braking resistors, CFW11 features a special braking method in vector control mode known as Optimal Braking®. This innovation delivers a high-performance braking torque without requiring a braking resistor.
SoftPLC Function
It is a resource that provides PLC features to the CFW11 without the addition of any accessories. It provides flexibility to the product, allowing the user to create his/her own applicative software (user’s program).
The SoftPLC main features are:
- Ladder language programming using WLP software
- Access to all VSD parameters and I/Os
- Configurable PLC, mathematical and control blocks
- Applicative software download, upload and online monitoring via USB connection
- Storage of user application in the CFW11 flash memory module (see below)
- Memory capacity of 15 kB for user application storage
Main Characteristics
- Power supply:
- 200 to 240 V single-phase: output current from 6 to 10 A (2.0 to 3 cv)
- 200 to 230/240 V three-phase: rated output current from 7.0 to 211 A (2.0 to 150 cv)
- 380 to 480 V three-phase: rated output current from 3.6 to 720 A (2 to 970 cv)
- 500 to 600 V three-phase: rated output current from 2.7 to 435 A (2 to 850 cv)
- 500-690 V three-phase: rated output current from 2.7 to 365 A (3 to 850 cv)
- 200 to 240 V single-phase: output current from 6 to 10 A (2.0 to 3 cv)
- Built-in inductors on the DC Link
- Space saving in the panel
- Built-in USB port
- Inverter smart cooling system
- Several communication protocols available (Modbus-RTU, Modbus-TCP, Profibus-DP-V1, DeviceNet, CANopen, EtherNet/IP, EtherCAT, PROFINET-IO and BACnet)
- Version with cabinet with degree of protection IP55 (versions with built-in switch-disconnector)
- High precision and reliability in speed and torque control
- Robust hardware
To learn more about the WEG line of products give your local Barry Sales Representative a call at 636-326-1211.
DC Drives
Parker DC Motor Speed Controllers
Parker offers a full range of drives including stepper, compact and high-performance servo, AC variable speed, high current output DC and panel mounted drives. Parker industry leading drives include Sensor less, Vector and Micro stepping options. Parker drives are suitable for speed, torque or position control and are available in power ranges from fractional to over 2,000 hp. Parker also offers inverters for renewable energy applications that convert DC power to AC electricity and deliver power to the grid, allowing hybrid vehicles and mobile equipment that convert regenerated power to battery storage to reduce fuel consumption and emissions.
DC Motor Speed Controller - DC590+Series
The advanced DC590+ series 4-quadrant variable speed DC drives offer current ratings of up to 2700A, function block programming, configurable I/O and extensive application software, meeting the demands of the most complex DC motor control applications.
Parker - AC20 Variable Frequency Drives
The AC20 Advanced Compact Drive is a highly featured yet economical solution to general purpose motor control applications. AC20 provides speed or torque control in the power range of 2 - 250HP. Its compact dimensions house many features normally only associated with system drives, including sensorless vector mode for control of Permanent Magnet (PMAC) and AC induction motors, encoder feedback and I/O expansion option cards, Safe Torque Off and an onboard Ethernet port that supports major industrial Ethernet protocols. AC20 provides the perfect solution for OEM machine builders looking for a compact, cost-effective drive without compromising on performance.
Features/Benefits
Simplicity
- Easy to configure with free Parker DSELite software tool
- Onboard Ethernet port for programming and communications
- Clear English language intuitive keypad for local setup and control
- No complex options/configurators - all features available in the base inverter
Wiring bracket simplifies installation
Safety and Reliability
- Conformally coated for harsh environment protection as standard
- Proven power stage design and technology
- Replaceable fans
- Safe Torque off: SIL2, PLd
- SD card slot for application backup
Parker - AC30 Variable Frequency Drive Family
NOW with Enhanced Capability, Connectivity, and Power...
Parker’s Electromechanical Division North America is pleased to announce the enhancement of the AC30 variable speed drives with the new P and D control modules for greater functional capability to meet the needs of advanced system applications. In addition, the AC30 power range for these applications has been increased from 100 HP to 350 HP with the release of the new J and K frames.
Updated firmware for the AC30P and AC30D offers new diagnostic features, on-board communications and support for closed loop control of PMAC motors.
New Products Features
- Open loop or optional closed loop operation with pulse encoder feedback module
- Ethernet TCP/IP as standard
- I/O expansion options
- Parameter Data logging to SD Card
- Enhanced 1588 Peer to Peer communications
- "Black Box" trip history recording
- PDQ Tool "Multi-Instance" capability
- Chassis or through-panel mount as standard
- System application libraries
- SMART diagnostics
- User customizable web server
- Dual encoder inputs
- 2 high speed mark registration inputs
Drives delivered with a previous firmware version can be updated through the PDQ software tool. The new PDQ is now available to download and is free of charge. Please contact your local Barry Sales Representative. You can download the AC30 Catalog and AC30 Features and Compatibilities Flyer below: